生产线平衡改善的四大方法
关键词:生产线平衡,现场管理,生产改善
生产线平衡
在介绍生产线平衡的概念之前,我们首先谈谈木桶定律:
一个木桶盛水多少,并不取决于桶壁上最高的那块木板,而恰恰取决于桶壁上最短的那块木板。
三个推论
A. 只有桶壁上所有木板都足够高,木桶才能盛满水。
B. 所有木板高出最低木板的部分是没有意义的,而且高出越多,浪费就越大。
C. 提高木桶容量最有效的办法就是设法加高最低木板的高度。
生产线平衡与木桶定律非常相似:
生产线的最大产能不是取决于作业速度最快的工位,而恰恰取决于作业速度最慢的工位,最快与最慢的差距越大,产能损失就越大。
企业现场管理的整体水平并不取决于最优秀的车间单位而是取决于最差的车间单位,同理,对一条生产线来言,其产量、效率高低也是如此。
接下来我们来看看生产线平衡常见的五大概念:
一,节拍
节拍指在规定时间内完成预定产量,各工序完成单位成品所需的作业时间。
其计算公式为:
节拍 r = 有效工作时间 T ÷ 产出数量 Q
教科书上的一道习题是这样的:
某工厂每小时产出400台机器,计算其节拍(以秒/台 为单位)
r = 60s × 60 ÷ 400 台 = 9 秒/台
而实际情况是这样的:
某制品流水线计划年销售量为20000件,另需生产备件2000件,废品率2%,两班制工作,每班8小时,时间有效利用系数95%,求流水线的节拍。(其年生产天数为254天,节拍时间按分钟计算)
【解】
T效 = 254 × 8 × 2 × 60 × 95% = 231648 分钟
Q = (20000+2000) ÷ (1-2%) = 22449 件
r = T效 ÷ Q = 231648 ÷ 22449 = 11 分/件
二,生产线平衡
生产线平衡是指工程流动间或工序流动间负荷之差距最小、流动顺畅、减少因时间差所造成的等待或滯留現象。
平衡生产线能发挥的作用有很多:
通过平衡生产线可以综合应用到程序分析、动作分析、layout分析、搬动分析、时间分析等全部IE手法,提高全员综合素质;
在平衡的生产线基础上实现单元生产,提高生产应变能力;
减少单件产品的工时消耗,降低成本(等同于提高人均产量);
减少工序的在制品,真正实现“一个流”或“单片流”;
提升整体生产线效率和降低生产现场的各种浪费;
消除人员等待现象,提升员工士气;
减少工序间的在制品,减少现场场地的占用;
可以稳定和提升产品品质。
它是生产流程设计与作业标准化中最重要的方法。通过平衡生产,可以加深理解“一个流”生产模式及熟悉“单元化生产”的编制方法。
那么如何实现生产线平衡呢?
保证各工序之间的先后顺序;
组合的工序时间不能大于节拍;
各工作地的作业时间应尽量接近或等于节拍;
使工站数目尽量少。
三,单元化生产(Cell Line)
单元化生产是精益思想的实践方式之一,是精益生产的重要组成部分。单元化即是将设备和厂房以特定的顺序安排,使材料和零件以最小的搬运完成部分或者全部生产过程。
其特点是:
产品不固定、Cell工位专业化程度低,可以灵活转换生产其他产品;
工艺过程封闭,单元内工位可以按工艺顺序安排为流水形式,也可以一个工位独立完成所有工序。单元内可以有很短小的流水线;
生产没有明显的节奏性。可以间断,可以连续。
▼ 根据生产需求变化进行有弹性的生产线布置 ▼
四,标准工时
标准工时是指一个熟练工用规定的作业方法以标准速度进行作业时所需的作业时间。
其计算公式为:
标准工时 = 正常工时 + 宽放工时
= 观测工时 ×( 1 + 评价系数)+ 观测工时 × 宽放率
其中,
观测工时 = 某工序的若干个观测时间的平均值
评价系数 = 熟练度+努力度+……(常采用熟练度与努力度)
▼ 熟练度 ▼
▼ 努力度 ▼
▼ 宽放率 ▼
五,生产线平衡率
其计算公式为:
平衡率 = 产品标准工时 ÷(瓶颈岗位时间 × 人数)× 100%
生产线平衡损失 = 1 - 平衡率
其中,
产品标准工时指的是每个工位所用时间的总和,其计算公式为
产品标准工时 = ∑(T1+T2+……Tn)
一般要求生产线平衡率达到85%以上。
我们来看一个实际应用:
请问哪个的平衡率更好?
【解】
电装3人平衡率 =(32+37+40)÷(40×3)× 100% = 90.8%
电装7人平衡率 = (18+18+24+37+45+16)÷(45×7)× 100% = 49.5%
同样的产品,因工序组合及布局的不同导致平衡率的差异。平衡率较差时,需反思工序规划的合理性。
如果你是工厂负责人,接下来,你要做什么?你准备怎么做?
平衡改善
首先对生产线平衡进行分析:
1,确定对象与范围
2,用作业分析把握现状
3,测定各工序的净时间
4,制作速度图表
5,计算平衡率
6,分析结果并制定改善方案
改善应该遵循以下原则:
1,首先考虑对瓶颈工序进行改善
2,改善耗时长的工程,缩短作业时间
3,改善耗时较短的工程
常见分析方法
程序分析法(ECRS):整体性制造过程各作业运用剔除、合并、重排与简化使之合理化。
▼ ECRS原则 ▼
▼ ECRS法运用图示简介 ▼
▼ 工序价值思考 ▼
操作分析法:是对某部分的作业分析操作者的作业方法,或与机器的关系达到改善作业方法,降低工时消耗,提高设备利用率。(常分为:人机操作分析、联合操作分析、双手操作分析)
动作分析法:对操作者细微身体动作进行分析,删除其无效动作,提高生产效率
▼ 吉尔布雷斯动素表 ▼
▼ 有效动素与无效动素 ▼
动作经济改善原则
动作经济原则共二十二项并归納为下列三大类:
1. 关于人体之运用:
双手应同时开始并同时完成其动作;
除規定时间外,双手不应同时空闲;
双臂之动作应对称,方向并同时作业;
手之动作应用最低等級而能得到滿意結果者为妥;
物体之动作量应尽可能利用之,但如需肌力制止时,则应將其减至最小度;
连续之曲线运动,较含有方向突变之直线运动为佳;
弹道式之运动,较受限制之运动轻快确定;
动作应尽可能使用轻松自然之节奏,因节奏能使动作流利及自发。
2. 关于操作場所布置:
工具物料应放于固定处;
工具物料及裝置应布置于工作者之前面近处;
零件物料之供給,应利用其重量堕至工作者手邊;
[堕送]方法应尽可能利用之;
工具物料应依照最佳之工作順序排列;
应有适当之照明设备,使视觉滿意舒适;
工作台及椅之高度,应使工作者坐立适宜;
工作椅式樣及高度,应可使工作者保持良好的姿勢。
3. 关于工具设备:
尽量解除手之工作,而以夾具或足踏工具代替之;
可能时,应將两种工具合并为之;
工具物料应尽可能预放在工作位置;
手指分別工作时,其各个负荷按照其本能,予以分配;
手柄之设计,应尽可能使与手之接触面积增大;
机器上杠杆,十字杠及手轮之位置,应能使工作者极少变动其姿勢,且能利用机械之最大能力。
4. 动作经济改善四大原则
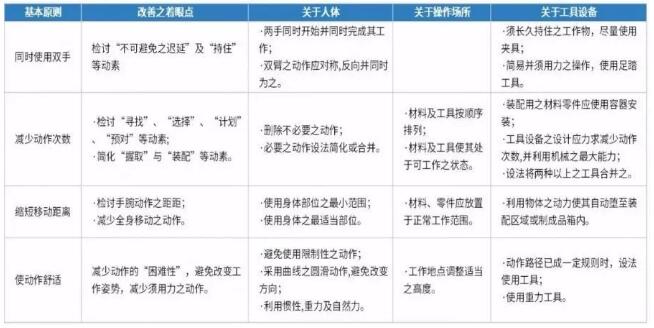